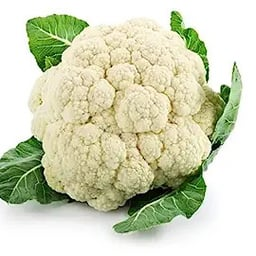
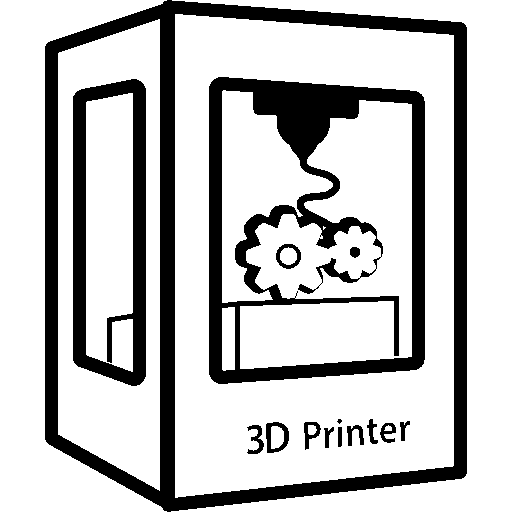
Interesting… I didn’t know purge filament existed. In fact, I wondered what would happen if I ever ran something that truly gummed up the nozzle, if I’d have to replace it entirely or something.
Interesting… I didn’t know purge filament existed. In fact, I wondered what would happen if I ever ran something that truly gummed up the nozzle, if I’d have to replace it entirely or something.
Resin is well within reach of the casual hobbyist now - we’re talking a couple hundred dollars to get an entry level machine, and a little extra coin for the materials/consumables. I have a (now old) Mars 3 that is ticking along beautifully
I am very tempted by a resin printer. However - and this is going to sound weird - I actually like the limitations of FDM.
And this is why: I’m a hacker at heart (in the old sense, not the nasty illegal stuff) and I like to push the envelope of what our Prusa Mk4 printer can do. I’ve printed stuff with that thing that I had no right to print by working the workarounds in the model, playing with layer sizes and controlling the path of the nozzle so it ends up printing features that are right at the limit of what it can do. Hell, even the hinges in those specs of mine are kind of pushing it.
And it’s fun! It provides hours of good fun trying this or that and finally getting the little printer to print something right.
A resin printer would make very good prints without anything to do, if that makes sense 🙂
Also I want to work with different materials. I’m actually looking into getting a Prusa XL with several heads to combine TPU for flexible, hollow parts and PLA for the supports inside the parts. That’s something a resin printer can’t do: resin printers print… well, resin.
And finally, I’m always kind of designing parts with a view to making it available to anybody who has any old printer at home for them to print and enjoy. That approach entails designing for the lowest comon denominator (to a reasonable degree), something a resin printer is not.
So you see, while I would like a resin printer, I feel it’s just not the right printer for me.
tweak and reprint the frame a bit to match the lenses. That’s not really the end of the world, but I don’t count on any opticians to understand that
Oh believe me, they understand perfectly.
Here’s the thing - and I’m not inventing this: my current optician is a friend and she told me this verbatim: an optician’s bread and butter is selling you frames, and the services around fitting the lenses on the frame and fitting the frame on you. Opticians make almost no money on the lenses - which they have made abroad in developing countries usually.
I don’t deny that there’s a lot of measuring prior to ordering lenses, counselling the customer, and then a lot of fiddling with the temples and the nose pads after the glasses are completed to make sure the glasses are comfortable and yada-yada. The services provided by opticians are definitely useful, particularly for young wearers and for people who change frames often.
But really, if you’re a lifelong glasses wearer, you’re reasonably handy and you settle on one frame geometry, those measurements never change and you just don’t need the services.
Me, the last time I needed an optician’s services was over 20 years ago when I made my first frames out of nickel silver. Since then, I’ve only made copies of those exact frames because I really like them - including those 3D-printed ones I drew a few weeks ago: they’re a bit different to account for the nature of the 3D-printing process, but the key measurements are the same.
So whenever I go to an optician to order new lenses - which you almost have to because you can’t order the lenses direct, even if you have all the measurements needed by the lens maker, the convo always goes something like this:
I kid you not, it’s extortion. They hate it when you can do their job yourself so they charge you for the privilege. And since you don’t have access to their suppliers (they look out for each other) you have to go through them.
That sounds like a great idea!
In fact, an even better idea would be to split the lens in the plane that contains the crest of the bevel (which isn’t at the center of the edge all around). That way, the widest point would be on the bed for both halves, totally eliminating any overhang.
I’ll try that tomorrow. Thanks for the idea!
Lol
Clearly that’s progress 🙂
Thanks for the offer! But actually I didn’t model that part for me but for others who need a model of a finished lens. I already have real lenses myself.
The thing is, I shared the design of my glasses for others who might want to print themselves the same glasses too, and there seems to be enough interest that some folks printed them and went to their opticians with it, only to be turned away because the frames are unusual - or they didn’t want to risk having lenses made using the lens template only to find out that the lenses are unusable in the final frames - and they didn’t want to risk filing a notch in the lenses either, which is something that’s not usually done to fit lenses to frames.
And I can understand the opticians too: if they agree to order lenses and they don’t fit the frame, the loss is on them and they don’t need the aggravation.
I wanted to provide a model of a lens that those folks could print out of PLA to convince the opticians that it’s not sketchy or far-fetched. If this parts needs a resin machine - which, I agree with you, it absolutely looks like it does if you really want a quality part - then it sort of defeats the point of self-sufficiency of my little project.
Well, I toyed with the printer’s temperature settings until I found a combination of nozzle temperature and bed temperature that finally made it spew out parts without making a disaster.
It seems to flow best at 260C, but then when it lands on the bed, it immediately shrinks as it cools and the part curls up and comes unstuck. I had to lower the temperature to 245C and raise the bed temperature to the maximum this printer does - 110C - for the part to stick enough to complete.
The nozzle clearly isn’t hot enough because some layers on the final parts look like they’re about to delaminate. But any hotter than that and the material curls up. And it doesn’t matter what bed plate I use: that stuff doesn’t seem to stick to anything properly.
I printed spectacles with that mystery filament. You can see how floppy it is here:
https://toobnix.org/w/qJJ1htb9eqmiHx7gSpq2RT
It looks like TPU alright, but the temperatures involved aren’t really typical of TPU. Also, acetone does nothing to it whatsoever.
The material also doesn’t like to be filed or sanded, and the best results for a nice finish without bits of material sticking out all over the place is to “polish” it by running a very sharp x-acto blade across the surface until all the junk is gone and the surface is shiny.
Weird filament. Kind of useless…
It has a long piece of 1mm piano wire running through that acts as a spindle. It’s a standard hinge design called a continuous hinge. I suppose I could have 3D-printed the spindle but it would have made the hinge huge and not very nice-looking.
That’s kind of my problem: my correction is not simple. I can get near or far lenses with my correction for relatively cheap - like $100 a pair. But progressives are eye-wateringly expensive.
As for my frames, they’re both free and priceless to me because I make them myself. And just because they’re not off the shelf, they’re more rewarding to wear.
So having some understanding and control of that part of the process could have helped.
The only things you can rely on with regard to how the lenses are edged is:
The bevel will be “bevelly” - meaning it’ll be a bevel of some kind, between 90 and 120 degrees, but no flatter than that. In other words, you can rely on having something to grip the lens with and that’s enough.
The bevel follows the curvature of the frame. If you frame is flat, the bevel will be placed all around the edge of the lens flat too.
As much as your correction will allow, the bevel will be placed as far forward as possible so the lens looks like it’s tangent with the front of the frame all around, and all the thickness will be hidden at the back of the frame. So if your frame is, say, 2mm in width, the root of the bevel will be placed 1mm from the front of the edge.
The other thing you can rely on is that the bevel will be slightly oversized so they can be snapped into the frame, and the amount of oversize will be a bit higher for plastic frames which are more flexible. And that’s where the danger lies: if your frames are designed to hold the frame without pressure like mine, you have to tell the optician so they pass the information to the lens cutter. Otherwise you will received lenses that are slightly too big.
But don’t sweat it too much: the great thing with 3D printing is, even if the lenses you received aren’t the right size, you can always print another frame with slightly revised dimensions.
And if you really don’t want to print another frame, don’t forget that you pay beaucoup bucks for those damn bits of plastic, so you can always copiously warn the optician that your frames are not made of the kinds of plastics plastic frames are usually made of, and then the onus will be on the lens maker to make the lenses right for your frames (remember that they will be sent your frames, so they’ll know rightaway if the lenses fit).
If the lenses aren’t right, it’s their problem and you can reject the lenses and tell them to try again. If you warn the optician in no uncertain terms that your frames are PLA, they or the lens maker can’t claim they didn’t know.
Just design the frames you want with the shape you want, with a 120-degree bevel, and ask your optician if it’s workable for the lens maker. They might tell you they’ll ask them - and you can leave them a test print too if they want to sent it to the lens maker too. There isn’t much more to this really.
I’ll definitely add cable temples to the list of things to try and see what works well.
Be aware that cable temples are a lot more finicky to adjust than regular curved temples. If they’re too short, even a little, they’ll dig into the skin behind your ears and you’ll hate them. Likewise, if the hook is too narrow, the tip will hurt you under your ear.
That’s a big reason why cable temples went out of favor in the 1920’s: they’re great when they’re well adjusted, but they quickly become nasty and uncomfortable when they aren’t - unlike maladjusted curved temples which can simply ride up the ear a little without too much drama.
With regular metal wire, you can bend the temples this and that way to make them fit. Not so much with PLA. You can shape it with heat but if you do it more than once, it becomes rough and unpleasant to wear - if the PLA doesn’t delaminate completely. So take the time to design the right length and shape directly in your model. It’s a bit long and tedious but once you know the right dimensions, you’ll love how natural they feel.
Also, don’t make the wire too thin or it will dig into your skin as well. And too thick will make the wire inflexible and difficult to put on. The wire profile that works best for me is this (for PLA):
They’re prescription glasses. They’re my regular glasses I wear every day. I made the frames but I can’t print optical lenses, sadly. I wish I could because they cost a fortune and they’re a real rip-off…
Halting the print to insert the magnets would be problematic: I print on the company’s printer and it’s a 5-hour print, so I start it before going home in the evening to avoid annoying everybody during work hours.
We’re allowed to use the printer for personal prints. But the rule is, if someone arrives at the office and needs to print something for work, whatever private stuff is in the printer is removed to make way for work things. And of course, if the printer is running - or paused waiting for someone to attend to it - the print is cancelled.
So I’d have to arrive really early in the morning to make sure I get there before the most early birds but there are no buses at the wee hours of the morning. Therefore realistically, my long prints need to complete unattended and be ready to be chucked out in the morning if I’m not first to arrive at the office.
But I’m not worried about the magnets coming out: the fit is tight and I use really strong epoxy. I’ve yet to see anything assembled with that stuff come undone.
Thanks!
I just made one initial print but I didn’t leave enough free play in the frame holder at the bottom of that case, so while it worked, it was kind of a pain to insert the frames into it. I widened the play from 0.4 to 1.5 mm and now there’s zero usablility issue.
Another unexpected problem I discovered with that first print is that I couldn’t tell the top shell from the bottom shell when the case was closed. I completely overlooked this and it turned out to be a massive PITA: 50% of the time, I would open the case upside down. Silly eh 🙂 It seems obvious in hindsight.
But I like the symmetry of it. So I added “engraved” text at the front edge to tell if the box is the right way up before opening, and put my name and a description of the particular correction in that case as a bonus.
The rest - stiffness, hinge, lid fit. magnet fit - came out okay the first time out. I’m getting really good at knowing the printer’s tolerances in advance and leaving enough play for things that shouldn’t assemble with an interference fit.
Sounds like OptiBoard
The name rings a bell. Admittedly, I started looking into that stuff well before social media was even a thing 🙂
I didn’t realize you worked with a lens maker directly and not through an optician
Sorry I thought you meant to choose frames and for fitting. For that, I do my own, obviously.
But yeah, to order the lenses, I do have to go through opticians. And yes, they did measure my pupillary distance (only once, I’m not a shape-shifter), they do issue the order for the lenses in the correct format and they double-check the lenses when they arrive. Some of them tried to make me pay an extortion fee of $50 or something for bringing my own frames, but considering they wouldn’t be doing any added-value work beyond ordering the lenses for me, I thought that was a bit rich so I went elsewhere.
I did order lenses direct from Hoya once, because I had a friend who worked there. But apparently they found out and my friend told me never again, or he’d be in trouble. So now I go through my local optician when my prescription changes - which isn’t that often: the lady who owns the store knows me well, she’s kind of amused to see my various eyewear contraptions and she knows she’s never going to extract a fortune out of me, but also she doesn’t have to spend any time on me either. So she passes her supplier’s costs onto me almost without any surcharge.
I’m surprised to read that superglue is sometimes used
It’s only for round lenses, either in light-fitting frames, for safety in case the screw backs out in metal frames, or in plastic frames because plastic is a bit more slippery. Round lenses typically shift when you clean them with a little too much gusto and it can happen surprisingly easily even in well-fitting frames.
Glue is not ideal but sometimes it’s needed. And obviously it’s never used with non-round lenses that are always naturally oriented properly.
Without the simulated weight, they’re fine. But with weight, they slip off if I look down.
Firstly, are you sure those test lenses you’re using are polycarbonate? If they’re glass, they’re a lot heavier. And of course they might be thicker than necessary for your prescription because they’re cheap: thin lenses are lighter but more spendy.
But essentially you’ve discovered why I always wear glasses with cable temples 🙂 Yes, they’re a bit more annoying to fit in a case, but they hold your frames put on your nose and you never have to worry about your glasses slipping ever again.
Although the 3D-printed glasses I designed fold the temples at an angle to position the wires more smartly, so they fit in regular cases. And I’ve just finished designing a very nice 3D-printed custom case for them too, which I will publish on my Github soon. But here’s a sneak preview:
Also, I’ve been wearing cable temples for so long that the nose bridge of all my glasses, which all land more or less at the same place on my nose all the time, ended up leaving a permanent indent in my skin. So the nose bridge always fall in it now. I could almost do away with the temples and the frames wouldn’t even move at this point.
I think there isn’t an inexpensive way to do that.
If you don’t intend to change the shape of your frames, the easiest is to design around old lenses you have lying around. If you screw them up, you weren’t doing anything with them anyway so it doesn’t matter. And presumably they used to be as nice lenses as you could afford when you wore them, so they should be close to the new ones you’ll order after you’ve finished your design.
it’s good and comparable to professional CAD software. But the learning curve is dumb
I have to agree on that. I feel I can only use FreeCAD because I’ve taught myself SolidWorks years ago and I know what to look for when I want to achieve something. Or said another way, when I want to do something in FreeCAD, my though process is always “In what roundabout, convoluted way can I do in FreeCAD what I used to do in 2 clicks in SolidWorks?”. The only reason it works for me is because I know it can be done and I know the intuitive way it should be done.
I kind of have the same issue in Blender: I’ve been trying to teach myself Blender for years, but no matter how hard I try, it’s just not letting me in. Unlike FreeCAD, I have never known any other software similar to Blender, so I don’t know what I’m doing - or rather, what I should be doing - and it’s excruciatingly frustrating.
Haha so many questions 🙂 Thank you for your interest in my little project.
To address you questions:
Is there some forum where people discuss this? For tips and common pitfalls.
There is not. Not to my knowledge anyway.
The few usetul forums I found are reserved for people who work in the eyewear trade and they don’t want you to participate. I tried joining by pretending to be a professional, but they either found me out by asking where my store was, or because I asked questions that no true professional would ask.
What I know, I picked up over the years (decades really) making my own frames. But the opticians don’t like it when you make your own frames, because selling you frames is their bread and butter. They make almost no money selling you lenses. So they won’t help you undercut their business, that’s for sure.
You talked about the registration tab at length. I’m making mine not entirely radially symmetric. Does this mean I don’t need them? Will the lens wabble inside because its PLA?
Your correction may or may not need orientation.
If you have a simple myopia or hyperopia correction, it doesn’t matter how your lenses are oriented.
If you have astigmatism however, your correction has an axis and the lenses need to be oriented correctly to within a couple of degrees. You can see if your correction has an axis in your prescription: it looks like an arrow with an angle.
Progressive lenses are also oriented, because near is at the bottom and far at the top.
With non-round lenses, that’s not a problem: the edging machine will measure your frames and cut the lenses so they’re oriented correctly when mounted in the frames. You can’t really mount them any other way.
With round lenses - or near-round - like mine, the lenses can turn in the frames and you need some way to prevent that. Round frames are really the worst possible choice if your correction is oriented. But hey, I like them 🙂
Traditionally, if the frames are made of metal, the hoops can be closed with screws, and tightening the screws clamp the lenses and prevent them from turning. With plastic frames, in which lenses are traditionally clipped - possibly after heating the frames a bit - the fit may be tight enough for the lenses to stay put on their own. If not, usually the optician will drop a drop of superglue at the edge.
Also, typically with round frames, the lens maker or the optician will make a very small, almost invisible mark on the lenses to find the correct orientation should the lenses move. If your glasses are round, look very carefully around the edge of the lenses and you should see the mark - usually next to something obvious like the hinges.
If your optician didn’t make a mark, they probably figured they’d measure your correction again to find the optical axis on each lens (they’ll draw 3 dots on each lens) and then they’ll line up the 6 dots. But it’s longer and more annoying than leaving a mark.
With my metal frames - which I made myself - the lenses are clamped hard in the hoops. No problem.
With my 3D-printed version, PLA is much too weak to take a thread to tighten the hoops around the lenses with screws (or take inserts) and printing hoops that lenses can clip into securely without opening them up is really fussy (I know, I did it for a friend’s glasses I reproduced out of PLA). And I sure as hell didn’t want to use superglue on my super-expensive lenses - not to mention, I want to be able mount them and remove them in minutes with no efforts.
That’s why I designed split hinges that close around the lenses when mounting the temples, and this registration tabs system to lock the lenses in place without applying pressure on them.
If your correction doesn’t need orientation or if you’re designing non-round frames, you totally DO NOT need the registration tabs. It’s only for round, oriented lenses.
Does the frame slip more than with other material? Or maybe with a riding bow make it not noticeable.
In my design, yes, because like I said, the lenses are held in the hoops with almost no pressure. without the tabs, they turn very easily.
If you design non-round lenses, they might “creak” a bit if you try to turn them forcibly and the frames don’t fit very tight around the edges. But they won’t slip.
If you’re designing clip-in frames and the fit is correct, they won’t move whatsoever. But you’ll need to print several versions of the frames with a few dimensions adjusted ±0.05mm here and there to find the right size to clip in the lenses with no major drama, yet with enough pressure for a proper fit. It’s really quite a lot of fuss.
Was the optician able to bend the temples with heat or was no frame adjustment needed at all?
I never go to the optician 🙂 I like being independent for things I need in my life (I’m also a partial foot amputee and I make a lot of my own shoewear for the same reason).
I used to adjust my 3D-printed frames a bit with a hot-air gun. It didn’t take long but I didn’t like the repeated trial and error process. So I took the time to work the adjustments in the FreeCAD models, as I explained on my Github, so the final frames fit my face perfectly without any adjustment, right out of the printer.
The only thing I do is polish the nose bridge with 600-grit sandpaper to smooth out the “staircase” a bit (layers of PLA deposited at a 45-degree angle) and then chemically-polish it even smoother with acetone. I also chemically-polish the inside of the ear hooks but only when I print them with certain PLA filaments I have that always end up a bit rough for some reason, if it’s a pair of glasses I intend to be wearing for many hours continuously, so the hooks don’t irritate my ears. But usually with most filaments, I don’t have to: the wires are very smooth naturally out of the printer.
You’ve made the lens groove in this triangle shape. Is that the standard or will the tracer edger pick up any shape there? How’d you decide how deep to make that groove?
There are many types of bevels. But that type seems to be the most common for “regular” prescriptions on fairly flat or slightly curved frames. Depending on how thick your lenses are at the edges, the bevel is placed more or less forward by the edging machine to hide as much of the thickness as possible at the front when the lenses are mounted in your frame.
Usually grooves for that type of bevel are called “hide-a-bevel” grooves or V-grooves in the literature. They nominally have a 120-degree profile from what I could read. Although in fairness, I measured a few old lenses I had lying around with a profile projector and they measured between 90 and 120 degrees. So if it’s a standard, it’s not a very well respected one.
There are other types of grooves. The frames I made for my friend for example didn’t have a groove at all: the groove was a 0.6mm square groove in the edge of the lenses themselves, and the bevel was inside the frame hoops. Very strange! I had never seen this kind before.
There are also chopped bevel profiles for ultra-thick lenses, and “shelf bevels” for wraparound lenses, etc… Look it up: there is an almost infinite number of bevel types. And that’s just for solid frames: if you frames have a wire at the botton of the lenses, then the top half of the lenses have a bevel and the lower half have a groove. The variety is bewildering.
Lens makers usually look at your frames and mount the grinding wheel(s) with the correct profile(s) in the machine - or if the machine is fully automated, the tool changer loads the correct grinding wheel(s).
Often, they don’t even need to look at the frames: if you chose a standard model at your local optician, more often than not, both the frames and the lenses are sold by the same supplier - and usually they’re in Vietnam or somewhere all the way around the globe, which is why eyeglasses take so damn long to make, in case you wondered 🙂 But I digress…
Anyway, one thing you can count on with almost absolute certainty is that all edging machines are capable of cutting a “hide-a-bevel” 120-degree bevel. That’s why I chose that “standard” for my frames.
As for the depth, you don’t really choose it: it depends simply on the width of the hoop. My hoops are 2-mm in width, which results in a ~0.5mm depth because of the angle. I indicate it in the picture on my Github for redundancy, just in case, but it’s not strictly needed: all the lens maker needs to know is that’s it’s a bog-standard 120-degree bevel, to load the correct grinding wheel into the machine, or something close enough to that profile.
How comfortable do you find wearing PLA so far?
The glasses are SUPER comfortable. It’s not really because it’s PLA or some other material: it’s because the fit is perfect for me. It’s like shoes or clothes: bespoke always feels better.
If you take the time to design your own frames to perfection - be it 3D-printed or made using traditional methods - when you hit the right dimensions, you’ll know immediately: they’ll be the most incredibly comfortable glasses you’ve ever worn. And when you do it yourself, you have all the time in the world to make the fit as perfect as you want it to be, something opticians don’t have time to do because, well, they have to make their time worthwhile.
Finally, my glasses weigh 14 grams all told. That’s VERY light and it goes a long way towards making them comfortable. That’s definitely a plus and it’s entirely due to the 3D-printing process.
I hope the above answers your question 🙂 I wish you good luck with your own design endeavor
It’s getting quite good, and considering what I paid for it, it’s very very good indeed 🙂
It depends on your prescription, the material you choose, coatings and such. The shape of the lenses or the type of beveling have no impact on the price, unless they’re highly curved with a step bevel for instance.
My lenses are standard polycarbonate lenses with a basic scratch-resistant coating. But I have astigmatism and I need progressives, so the lenses come out at $400. And usually I also order a pair for far and near (not progressive) and they’re like $200 per.
That’s the only problem with the registration tabs in my design: it requires notching the bevel of the lenses - meaning you have to work up the courage to bring a file to brand-new lenses you just paid a sizeable portion of your last paycheck for 🙂
It depends on the material and printer and the orientation of the hole. Vertical holes (or up to 20 degree from vertical if they’re angled) are the most accurate because you basically exploit the printer’s X and Y locating abilities. Horizontal holes will always end up ovalized because horizontally they’ll be correct, but vertically they can only have a dimension that’s a multiple of the layer height.
With the aforementioned Prusa Mk4 printer and PLA, all the vertical small holes I print usually end up under ±0.05mm / 0.002" from the desired diameter. If the dimension is very important (for example, holes for a pogo pin holder that needs to fit with interference, otherwise it would fall off) I’ll print it 0.1mm / 0.005" undersized and then I’ll ream the hole just enough to get the proper fit. It’s quick but not as quick as not reaming the hole obviously 🙂
Note that our printer is in a closed enclosure and that seems to make a difference for repeatability: if I leave the doors open, the diameter of the final hole varies a bit more. Nor a lot more but noticeably.
The more I look at it, the more I think that is in fact TPU. And in fact I’ve read somewhere that most varieties of TPU are in fact impervious to acetone. The one roll I have here isn’t, but maybe this yellow piece is such a kind.